The Science Behind Porosity: A Comprehensive Guide for Welders and Fabricators
Comprehending the elaborate systems behind porosity in welding is essential for welders and producers pursuing impressive craftsmanship. As metalworkers delve right into the depths of this sensation, they reveal a globe governed by different variables that affect the development of these minuscule voids within welds. From the structure of the base materials to the details of the welding process itself, a plethora of variables conspire to either aggravate or reduce the existence of porosity. In this detailed guide, we will certainly decipher the scientific research behind porosity, discovering its results on weld top quality and unveiling progressed techniques for its control. Join us on this trip through the microcosm of welding imperfections, where accuracy meets understanding in the quest of perfect welds.
Recognizing Porosity in Welding
FIRST SENTENCE:
Examination of porosity in welding exposes vital understandings into the stability and top quality of the weld joint. Porosity, characterized by the visibility of tooth cavities or gaps within the weld metal, is a typical concern in welding processes. These voids, otherwise effectively attended to, can jeopardize the architectural honesty and mechanical properties of the weld, leading to prospective failures in the completed product.

To identify and quantify porosity, non-destructive testing techniques such as ultrasonic screening or X-ray assessment are frequently utilized. These methods permit the identification of internal flaws without jeopardizing the stability of the weld. By assessing the dimension, form, and distribution of porosity within a weld, welders can make educated decisions to enhance their welding procedures and achieve sounder weld joints.
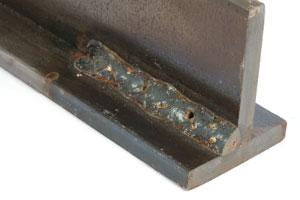
Factors Affecting Porosity Formation
The occurrence of porosity in welding is affected by a myriad of aspects, varying from gas securing effectiveness to the details of welding criterion settings. Welding parameters, consisting of voltage, present, travel rate, and electrode kind, likewise impact porosity development. The welding method utilized, such as gas steel arc welding (GMAW) or secured metal arc welding (SMAW), can affect porosity formation due to variants in heat circulation and gas insurance coverage - What is Porosity.
Results of Porosity on Weld Quality
The existence of porosity likewise compromises the weld's resistance to rust, as the trapped air or gases within the voids can react with the surrounding environment, leading to deterioration over time. Additionally, porosity can prevent the weld's capacity to withstand stress read here or influence, additional threatening the total high quality and dependability of the welded structure. In important applications such as aerospace, automotive, or structural constructions, where safety and sturdiness are critical, the detrimental effects of porosity on weld top quality can have severe effects, emphasizing the significance of lessening porosity through proper welding methods and treatments.
Strategies to Decrease Porosity
Furthermore, making use of the suitable welding parameters, such as the appropriate voltage, present, and travel speed, is vital in protecting against porosity. Maintaining a consistent arc size and angle during welding likewise assists decrease the likelihood of porosity.

Making use of the appropriate welding strategy, such as back-stepping or utilizing a weaving movement, can additionally aid distribute heat evenly and minimize the chances of porosity formation. By applying these strategies, welders can effectively lessen porosity and create top notch welded joints.
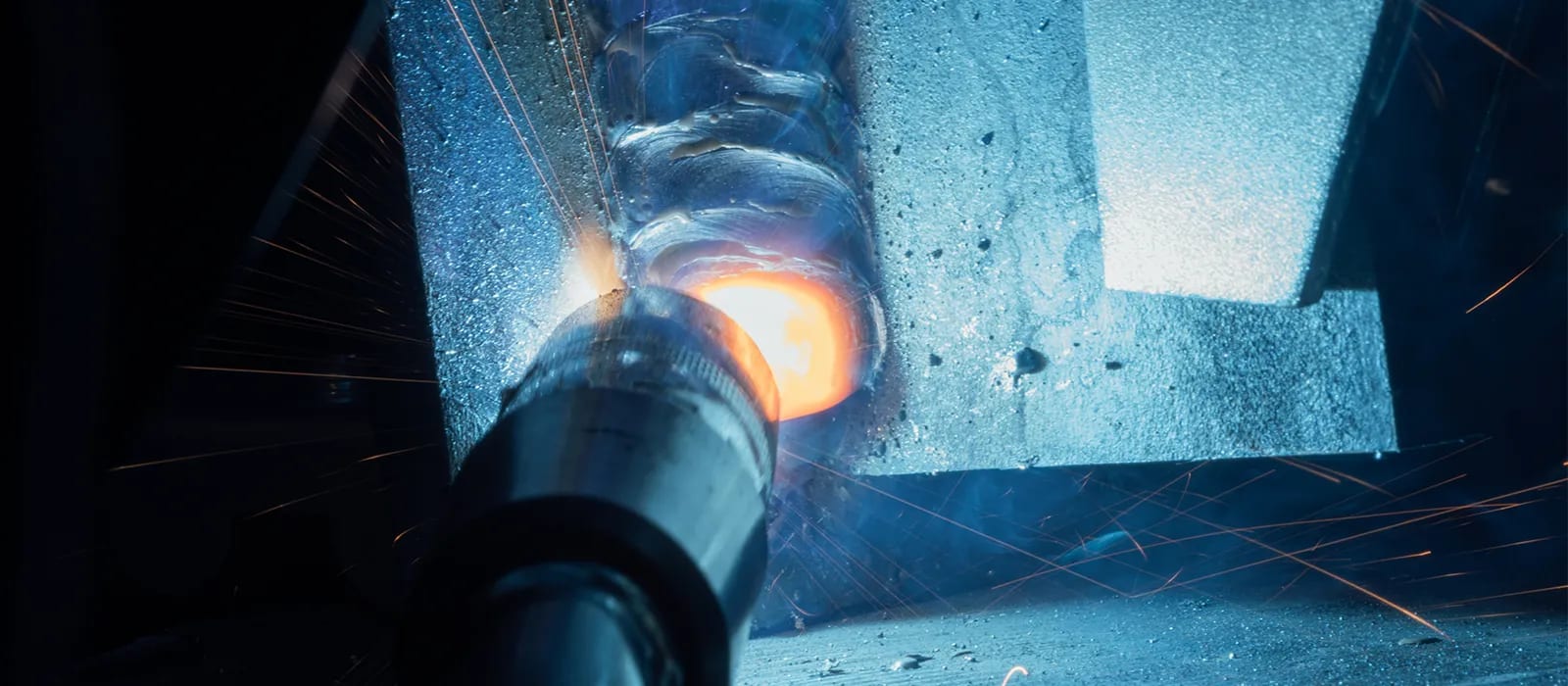
Advanced Solutions for Porosity Control
Implementing sophisticated technologies and cutting-edge techniques plays a pivotal function in attaining remarkable control over porosity in welding procedures. One innovative solution is making use of sophisticated gas combinations. Securing gases like helium or a combination of argon and hydrogen can help in reducing porosity by giving much better arc stability and boosted gas protection. Furthermore, employing sophisticated welding techniques such as pulsed MIG welding or changed environment welding can additionally assist minimize porosity concerns.
Another sophisticated service includes the usage of innovative welding equipment. For instance, making use of anonymous tools with built-in functions like waveform control and sophisticated power resources can enhance weld high quality and decrease porosity threats. The application of automated welding systems with exact control over criteria can significantly minimize porosity issues.
Additionally, integrating advanced surveillance and examination innovations such as real-time X-ray imaging or automated ultrasonic screening can help in spotting porosity early in the welding process, allowing for instant restorative activities. In general, incorporating these advanced services can substantially improve porosity control and improve the overall high quality of bonded components.
Verdict
In verdict, comprehending the science behind porosity in welding is important for welders and producers to generate Source high-grade welds - What is Porosity. Advanced services for porosity control can further boost the welding procedure and ensure a strong and trustworthy weld.